We detected, that your browser supports another language than the called one. This page is also available in your language! Would you switch to this page in your language?
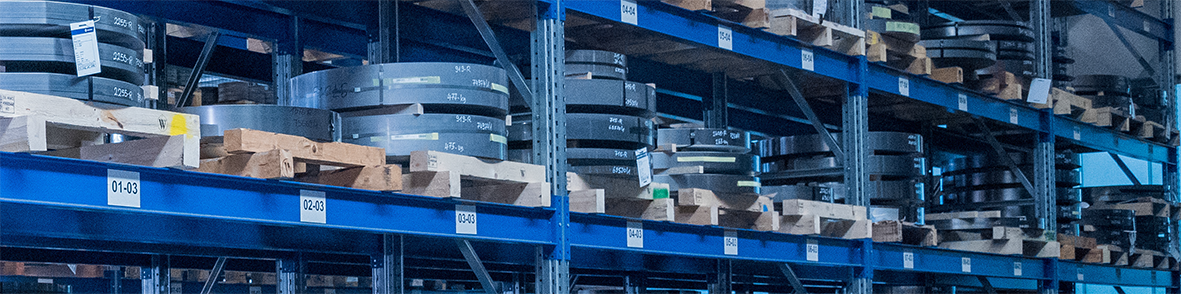
Standard materials
C60S (1.1211):
This spring steel is a quality steel according to DIN EN 10132-4. We use this spring steel exclusively for our original SCHNORR® safety washers and load washers according to DIN 6796.
C67S (1.1231) and C75S (1.1248):
These stainless steel grades according to DIN EN 10132-4 are used as cold rolled strip for disc springs of group 1 according to DIN EN 16983 up to a thickness of t < 1.25 mm and for our disc springs of the “K” series.
51CrV4 (1.8159):
This chromium-vanadium alloyed stainless steel is used in rolled condition (according to DIN 10132-4 or acc. to DIN 10089) for disc springs with a thickness between 1.25 mm to 6 mm. Normally this stainless steel is processed in forged form for disk thicknesses of more than 6 mm.
Materials for special requirements
Corrosive, high temperature and other aggressive environments require the use of materials. These materials, in general, have lower tensile strength than standard materials and should only be specified if absolutely necessary. These springs have a lower overall height than comparable sizes made of standard materials, resulting in lower spring force. This must be taken into consideration when using these materials.
Corrosion-resistant materials
X10 CrNi 18-8 (1.4310):
This chromium-nickel alloyed steel according to DIN EN 10151 is the most commonly used material for disc springs up to a thickness of t = 3.0 mm. Unfortunately, the cold forming process makes in magnetic.
X7 CrNiAl 17-7 (1.4568):
This steel alloy according to DIN EN 10151 is a precipitation- hardened spring steel which is processed in cold-strained condition up to a thickness of approx. 2.5 mm. The cold forming process makes this material magnetic.
X5 CrNiMo 17-12-2 (1.4401):
With this steel according to DIN EN 10151, the strength is somewhat less than that of the previous two. However, it offers higher corrosion resistance and lower magnetism. Small amounts of this material are hard to procure, and it is thus rarely used.
High-temperature materials
X22 CrMoV 12-1 (1.4923):
This chromium-molybdenum-vanadium steel according to DIN EN 10269 that can be quenched and tempered has proved very well for the use of heat-resistant disc springs.
X39 CrMo 17-1 (1.4122):
This is a chromium-molybdenum alloyed steel according to DIN EN 10088-2 that can be quenched and tempered. This material grade has also proved very well for the use of heatresistant disc springs.
Please bear in mind that both steel grades mentioned are not considered as corrosion-resistant steel grades.
Anti-magnetic and corrosion-resistant materials
CuSn 8 (2.1030):
Tin bronze according to DIN EN 1654 is an alloy consisting of copper and tin, maintaining its spring characteristics due to cold forming. Please bear in mind that the strength values and the spring forces resulting from it are considerably lower than with the standard material.
CuBe 2 (2.1247):
Copper-beryllium according to DIN EN 1654 is an excellent spring material grade which is suitable for extremely low temperatures up to the vicinity of the absolute zero point.
These copper alloys are absolutely anti-magnetic, and they have a very good electric conductivity. Furthermore they show a high corrosion resistance against many media.
Heat-resistant special materials with a very good corrosion resistance
Due to their composition, these nickel-base alloys show an excellent resistance against a lot of media. Unfortunately, they are expensive and often hard to procure. As these material grades are often used under extreme operational conditions, a potential creeping under load might lead to a loss of installation height/loss of force of the disc spring. This creeping is a function of temperature, time and tension. A disc spring can be used at higher temperatures, for example, when either a low load is chosen or the exposure time is accordingly short. Thus a maximum working temperature cannot be stated. The values stated in the material grade overview table can therefore serve as a guiding value only.
NiCr 15 Fe 7 TiAl (INCONEL X 750) (2.4669) and NiCr 19NbMo (INCONEL 718) (2.4668):
These nickel-chromium alloys are virtually cobalt-free and for this reason they are often used in nuclear reactor technology.
Materials Synoptic Table
With regard to the maximum working temperatures listed it must be taken into consideration that the setting height of the springs depends on the height of the tensions occurring and on the operating time on temperature. Furthermore, it has to be taken into consideration that with increasing temperature of the elasticity module of the material the strength diminishes. The operating temperature and thickness ranges can serve as reference values only. With heat-resistant steel grades, heat treatment and hardness deviate from the information given in the mentioned standards.
In case of any queries regarding material grade selection, please contact our engineering department.