We detected, that your browser supports another language than the called one. This page is also available in your language! Would you switch to this page in your language?
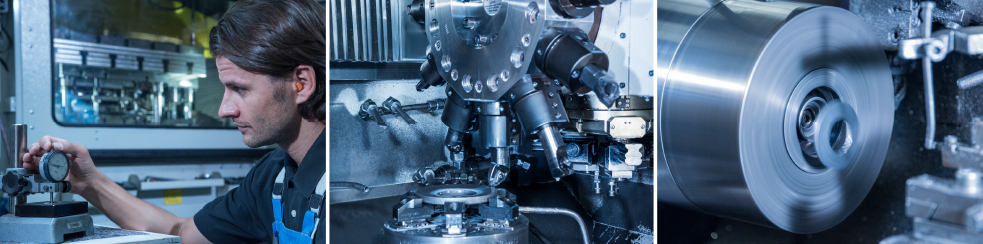
DISC SPRINGS
With effect from 01.02.2017 the familiar DIN standards for disc springs („DIN 2092-Calculation of Disc Springs“ and „DIN 2093-Quality requirements, Dimensions“) have been withdrawn.
These solely German standards have now been incorporated into European standards with the aim of securing the availability of high-quality standard disc springs for the whole world market.
- DIN EN 16983 – Quality requirements, Dimensions
- DIN EN 16984 – Calculation
Changes to content including any technical changes have not taken place by this measure. In this context we cite the following from the DIN EN 16984 und DIN EN 16983:
„as against DIN 2093:2013-12 the following changes have been made:
the German standard DIN 2093:2013-12 has been incorporated into a European standard with an unchanged technical content.“
„as against DIN 2092:2006-03 and DIN 2092 Modification 1:2007-08 the following changes have been made:
the documentation has been incorporated into a European standard with an unchanged technical content.“
These new standards are now in effect since 01.02.2017.
Classification
The large dimensional range in which disc springs are made requires different production methods. The methods employed range from simple stamping and stamping with extra machining to hot forged and rolled rings, which are turned or ground to obtain their final shape.
DIN EN 16983 (previously DIN 2093) specifies 3 manufacturing groups:
Group 1: Thickness t < 1.25 mm
Group 2: Thickness t = 1.25 to 6 mm
Group 3: Thickness t > 6 to 14 mm
Contact flats acc. to DIN EN 16983
Group | t | With contact flats and reduced disc spring thickness |
---|---|---|
1 | < 1,25 | no |
2 | 1,25 ≤ t ≤ 6 | no |
3 | > 6 < t ≤ 14 | yes |
Dimensional series
Dimensional series | h0/t |
---|---|
A | ~ 0,40 |
B | ~ 0,75 |
C | ~ 1,30 |
Overall height tolerances
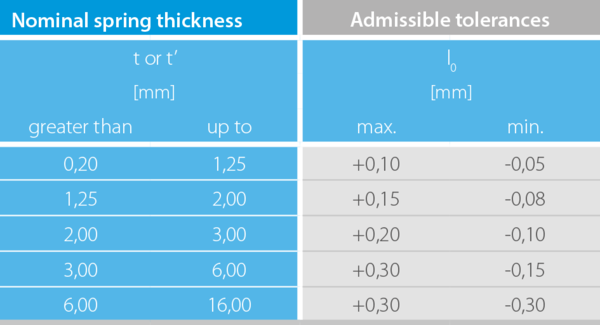
Allowances for the overall height with springs according to DIN EN 16983 (previously DIN 2093).
Diameter tolerances
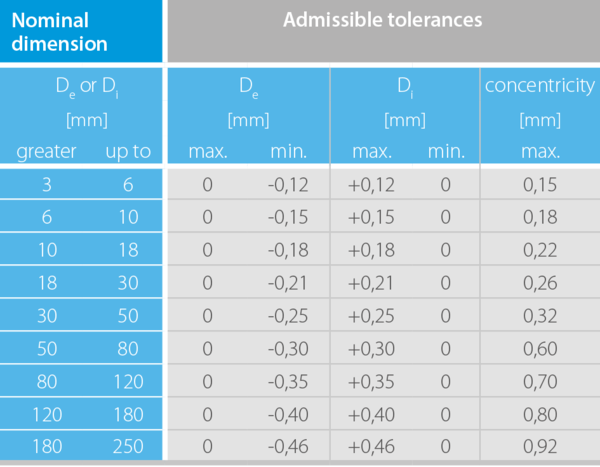
Allowances for external and internal diameters and concentricity with springs according to DIN EN 16983 (previously DIN 2093).
THICKNESS TOLERANCES
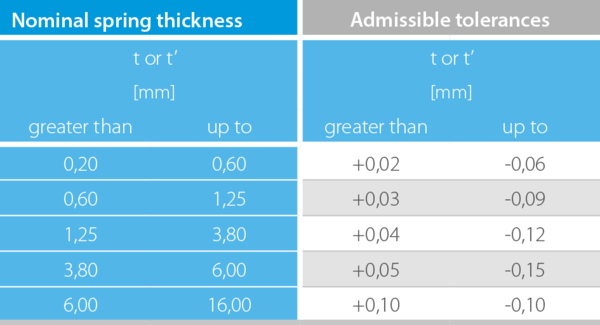
Allowances for spring thickness with springs according to DIN EN 16983 (previously DIN 2093).
LOAD TOLERANCES
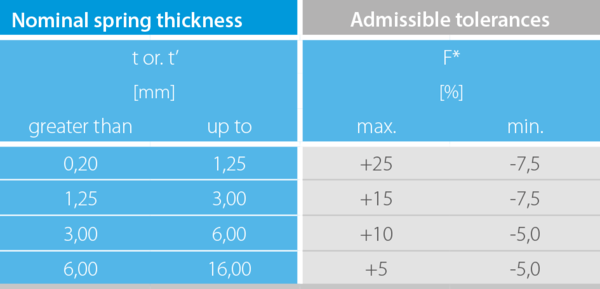
Allowances for the spring load with springs according to DIN EN 16983 (previously DIN 2093)
* F with test length lP = l0 – 0,75*h0 .
advantages
Compared with other types of springs, the disc spring has a number of advantageous properties:
- Absorption of very large loads within a small installation space.
- Linear, degressive or even progressive design of characteristic lines.
- Due to the almost unlimited number of possible combinations of individual disc springs, the characteristic curve and the column length can be further varied within additional limits.
- High service life under dynamic load (when dimensioned correctly).
- No relaxation (considering the permissible stress).
- Attainment of a large damping effect (considering the correct stacking).
- Because the springs are of an annular shape, force transmission is absolutely concentric.
POSSIBLE COMBINATIONS
The conical shape of the disc spring allows single springs to be combined in different ways. As a result, the characteristic of a spring combination can be varied in almost any way desired.
In principle the following possibilies exist:
- In spring columns with single springs stacked in series, the spring deflections add up with constant load (b).
- In spring columns with springs stacked in parallel, the forces add up at the same deflection (c).
- In spring columns with combinations of serial and parallel stacking, various characteristic curves can be realized (d).
If disc springs of different thickness are stacked in a suitable way, then even progressive characteristic curves can be realized. For this, either several disc springs of different material thickness or identical disc springs with intermediate rings of different thickness or different layering types are used.
Guidance of disc spring stacks
Disc springs always need a guide element to prevent lateral movement.
The guide can be on the outside De or the inside Di of the springs, but inside guidance on a bolt or shaft is preferred to the outside guidance in a sleeve, because it offers design and economic advantages.
The guide elements and abutments should be hardened if possible to a minimum of 60 HRC (minimum case depth of 0.8 mm). The surface of the guide element should be smooth and, if possible, ground. For static applications, guides can be unhardened.
For more technical information concerning disc springs we ask you to use our technical handbook.